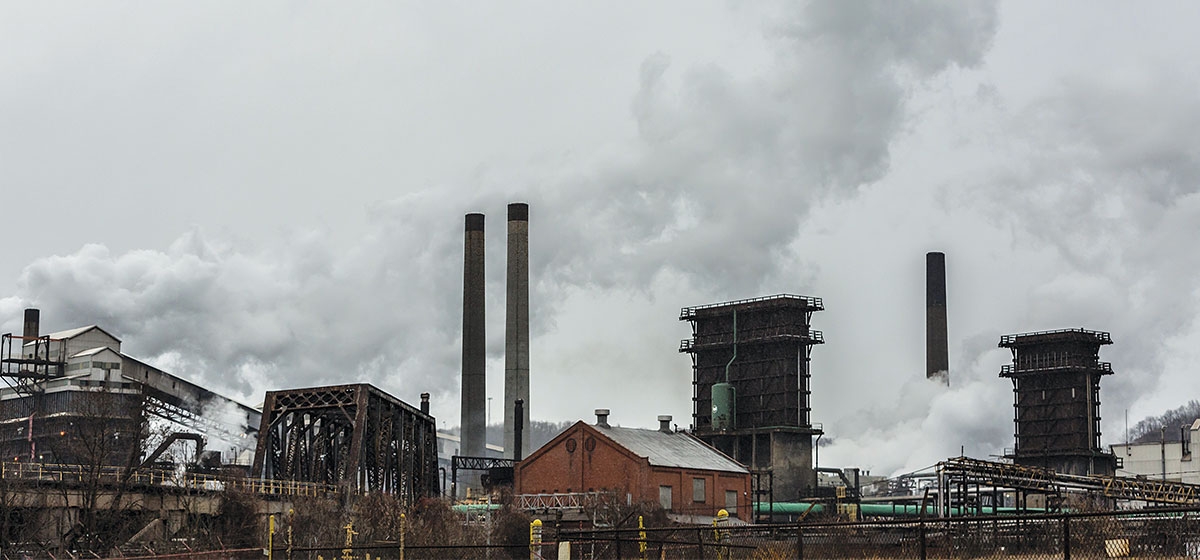
At the Clairton Public Library in the industrial Monongahela River valley, patrons can check out “Moby Dick,” “To Kill a Mockingbird,” the adventures of Curious George and any number of Nancy Drew mysteries. They can read issues of Vogue and Popular Science. They can take home the music of Elton John and Rihanna, or the recent best-picture nominee, “Fences.” And they can borrow a SPECK monitor to measure the level of fine particulate air pollution in their homes.
The pollution monitors are popular in Clairton. On one brisk weekday in March, eight of the library’s 12 monitors were out on loan.
Air quality is a concern in this Allegheny County city of 6,700 people. It is home to the United States Steel Corporation’s Clairton plant, the largest coke works in North America, employer of 1,100 steelworkers and the poster child of air pollution in southwestern Pennsylvania.
No plant in the region is more tightly regulated or more closely watched. The data collected on its emissions are voluminous. U.S. Steel spent hundreds of millions of dollars in the past decade on upgrades to reduce pollution released from the coke plant. Emissions levels have fallen. Air quality in the region has improved. Pollution recorded in nearby communities downwind of the plant is markedly lower.
Yet, the plant’s long history of violating air quality regulations and the county’s ongoing struggle to meet federal air quality standards provide a basis for complaints from residents like 76-year-old Gloria M. Ford. “The air here, it’s bad,” said the life-long Clairton resident. “I used to sleep with my windows open, until I started having a problem with breathing.”
The coke plant, which bakes 6 million tons of coal a year into fuel for steelmaking, is a major source of sulfur dioxide emissions, which can harm the respiratory system and make breathing difficult. Emissions of toxic chemicals—some of which are known cancer risks—totaled nearly 970,000 pounds in 2015, U.S. Environmental Protection Agency data show. In southwestern Pennsylvania, only the Keystone coal-fired power plant in Armstrong County released more.
And the coke works in Clairton continues to drive the level of fine particulate pollution, known as PM2.5, in much of Allegheny County—one of only 20 U.S. counties that fail to meet the federal standard for the far-travelling pollutant that research suggests increases the risks of respiratory illness, heart disease, stroke, cancer and premature death.
‘This was the place to be’
For better or worse, much of Clairton’s image and circumstance is owed to the U.S. Steel coke works, which has been a neighbor since 1904.
During peak years in the 1940s, some 7,200 union steelworkers were employed making coke in Clairton—a workforce larger than the city’s current population.
“A lot of families had three, four generations working there,” said Clairton Mayor Richard Lattanzi, himself a steelworker at the U.S. Steel Irvin Works in West Mifflin. The city held nearly 20,000 residents when booming. Its streets were lined with restaurants and bars and, unlike today, residents had three grocery stores to choose from. “This was the place to be.”
But like other Mon Valley mill towns, Clairton has endured decades of population decline. The reasons for the exodus included wage growth that made it affordable for workers to move to suburban bedroom communities developed in the 1950s and 1960s, and the collapse of the region’s steel industry in the 1980s and 1990s, when tens of thousands of jobs in the valley were lost and mills in McKeesport, Duquesne and Homestead became Rust belt brown-fields.
“A lot of families had three, four generations working there.” —Clairton Mayor Richard Lattanzi
Clairton’s population fell 54 percent from 1960 to 2000. At the same time neighbor Duquesne lost 51 percent, Homestead 52 percent, McKeesport 47 percent, Glassport 34 percent, and Port Vue 36 percent.
Local businesses withered. Property values tumbled. Tax revenues dwindled.
Clairton was declared a financially distressed community for 27 years under Pennsylvania’s Act 47 municipality recovery law until it was removed from the list in 2015 amid signs of stability and rising prospects. This year, the city received more than $3 million in state tax credits and corporate grants to invest in community and commercial district revitalization as it works toward shedding the image of a mill town in decline.
The coke works remains important to such hopes. The $300,000 to $400,000 in property taxes Lattanzi estimates the plant pays annually represents about one third of Clairton’s tax base. The fact that the plant continues to pay taxes shows its resilience in an embattled industry and at a time when U.S. Steel is moving to reduce its dependence on coal and coke.
Last year, the Clairton works became the last coke plant operating in the region when Ann Arbor, Mich.-based DTE Energy Services closed its Shenango coke works on Neville Island, citing flagging demand for its product.
In recent years, U.S. Steel has curtailed coke operations in Indiana and Illinois, and explored natural gas as an alternative to coke, as well as electric arc furnace steelmaking and other coke-less technologies. Reasons for pursuing such options also include the potential to trim its coke-making costs in the future, according to company Security and Exchange Commission filings.
Those costs at Clairton have amounted to more than $600 million in the past decade. Much of it was spent on two new low-emissions quench towers and C-Battery, a technologically advanced battery of 84 coke ovens that produces more efficiently and controls emissions more effectively than any battery ever built on the banks of the Monongahela.
Such investments have helped to reduce emissions of harmful pollutants from the plant and lower downwind pollution levels, Allegheny County air quality regulators say. But it has not been enough to prevent the plant from repeatedly violating its air regulations or to bring fine particulate pollution across the county in line with federal standards, particularly in the Mon Valley communities where relief is needed most.
A dirty business
The environmental nonprofit PennFuture last year filed notice in federal court of its intention to sue U.S. Steel for violating air quality laws at the Clairton works. As evidence, the nonprofit cited some 6,700 violations it culled from regulatory data over a 3½-year period ending in 2015.
Under the federal Clean Air Act, citizens are able to file such notices if they believe regulatory agencies are not enforcing air quality laws. Regulators are then compelled to take enforcement action within 60 days.
The Allegheny County Health Department, whose regulatory jurisdiction includes the coke works, announced a court-approved consent decree two months later requiring the company to make upgrades and repairs to correct the problems that allowed the fugitive emissions. The county also levied $25,000 in new fines.
It was a familiar enforcement process for Allegheny County and U.S. Steel—they’ve done it seven other times since 1990.
The county assigns a full-time team of air quality inspectors to the Clairton plant to supplement electronic monitoring and company oversight. Such surveillance makes it more likely the coke works will rack up more violations than other industrial plants where daily inspections are rarely if ever done.
“Coke facilities are the only facilities where we have inspectors,” said James Kelly, the health department deputy director who oversees the Bureau of Environmental Health. “You would have elevated compliance concerns at other facilities if you had inspectors there all the time.”
The Clairton plant operates under such scrutiny for good reason. As pollution sources go, none are more imposing than the coke works.
Coke has long been the fuel that lights the blast furnaces in steelmaking. The coke produced in Clairton fuels two other U.S. Steel Mon Valley Works plants, the Irvin Works and the Edgar Thomson plant in Braddock.
Making coke is a dirty business. Coal is loaded, or “charged” into a series of narrow, oxygen-free ovens, baked at 2,000 degrees Fahrenheit for about 18 hours and pushed as a molten mass into railcars in a burst of flame and smoke. It’s then doused with water in quench towers, which attempt to scrub the steam of pollutants before it is released from the stack.
It’s a recipe for hazardous byproducts that can become airborne public health concerns. Baking coal produces PM2.5, sulfur dioxide, and a number of air toxics, a list of regulated chemicals that includes benzene and other known or suspected carcinogens. Coke oven gas itself is one of them.
Moreover, the scale of the Clairton works is enormous. Ten batteries, each holding 60– 90 coke ovens, bake around the clock at the 390-acre plant to make about 4.3 million tons of coke a year. The shuttered Shenango coke works on the Ohio River, by comparison, operated only one 56-oven battery to produce 350,000 tons of coke.
Each coke oven offers pollutants opportunities to escape from doors and lids, as do the routine processes, such quenching super-heated freshly baked coke. All told, the Clairton plant has 6,000 individual points of emission from which pollutants can escape when technology, maintenance and oversight fails.
Trouble in the valley
In the 1970s, when the Mon Valley was lined with working steel mills, Bob Recaldini Sr. drove his 1968 Pontiac Bonneville through Clairton twice a day to and from his piano delivery job in Belle Vernon.
“It was a white car. But by the time I got home, it would look like this,” he said, tapping the faded pink lunch counter at Johnny’s Drive-In near the Clairton plant.
What was a nuisance to Recaldini continues to be a public health risk to residents in the Monongahela River valley, the county and beyond, air data and health studies suggest.
Cancer risks in Allegheny County from breathing air toxics, for example, are among the highest in the nation, according EPA assessments. When PM2.5 is the measure, the Pittsburgh metro area has the eighth least-healthiest air out of 176 U.S. regions, the American Lung Association reports. And local researchers are finding asthma rates among elementary school students in Clairton and two other Mon Valley communities to be much higher than national averages.
PM2.5 ranks as one of the most dangerous air pollutants due to its microscopic size, the harm it can cause in the body and the fact that it will travel as far as the wind can take it until it rains. As with many air pollutants, long-term exposure poses the greatest risks.
The particles are not homogenous. They can include fine dust from construction and grinding operations, smoke from wood-burning stoves, even the greasy exhaust from restaurant fryers. But the largest producers include cars, diesel trucks and buses, coal-fired power stations, and steel mills. No source in southwestern Pennsylvania is more prolific than the Clairton plant.
Wind, weather and topography influence how and where particulates travel and the exposure levels in the places they reach. Winds, for example, most often blow into southwestern Pennsylvania from the west and southwest, so pollution generally travels in that direction.
One consequence is that southwestern Pennsylvania gets a whiff of long-living pollutants, such as PM2.5, from the out-of-state power plants and factories in the Ohio River valley. The air quality monitor in South Fayette on the western edge of Allegheny County is an indicator of the quality of the arriving air. In 2015, the PM2.5 annual average there was 8.5 micrograms per cubic centimeter, lowest in the county. The federal limit is 12 micrograms per cubic centimeter.
The region’s hills and valleys also prevent air pollutants from being uniformly distributed. River valleys tend to hold the highest concentrations. They’re also prone to temperature inversions that force pollutants to sit over towns, usually from early evening until midmorning the next day.
Sitting at the bottom of a river valley greatly expands the Clairton plant’s pollution footprint. Another factor is the height of the stacks at the plant, where even recently built 160-foot quench towers don’t clear the rim of the valley.
“The stacks aren’t as high as the surrounding hills so the emissions don’t get out of the valley,” said Albert Presto, assistant research professor in the Carnegie Mellon University Department of Mechanical Engineering and a member of the school’s Center for Atmospheric Particle Studies. “In an inversion, the emissions sit and stew. There isn’t the dilution you would have with much taller stacks.”
“The stacks aren’t as high as the surrounding hills, so the emissions don’t get out of the valley.” — Albert Presto, Carnegie Mellon University, Center for Atmospheric Particle Studies
PM2.5 levels in Clairton, the municipality closest to the coke works, are nearly 20 percent lower than levels recorded on the ridge across the river in Liberty Borough. That’s because Clairton rests in a flat where prevailing southwest winds are less direct than in Liberty, where the county has an air monitor on the roof of South Allegheny High School. That monitor regularly records the highest levels in the county and is the only one to report levels that exceed federal limits.
Plumes of PM2.5 most often spread along the Mon Valley at night. “What typically happens is the mixing height is not very high, the emissions get stuck near the ground and the wind ever so slightly blows things toward you from the Mon Valley,” said Presto, who with his colleagues map air pollution trends with stationary and mobile monitors.
“The valley is the corridor for the pollution from Clairton. If you’re sitting in Squirrel Hill and the wind is coming up the river you will see it as an overnight spike. Here on campus, on some nights PM 2.5 and sulfur dioxide will be low. On some nights, everything will spike. And the spikes almost always occur when the wind is coming from the Mon Valley. You can get the same pattern in Mt. Lebanon when the wind is coming from the east.”
Negotiating pollution
Harnessing those emissions has proven to be an operational and engineering challenge so steep that the Clairton plant has not been able to do so to the degree necessary to avoid repeatedly violating air quality regulations.
The enforcement model used in the U.S. almost always gives plants like Clairton a chance to correct pollution-causing problems when they arise, regardless of how often that occurs. Like the EPA and state regulatory agencies, the Allegheny County Health Department negotiates with industrial polluters to improve their environmental performance. The resulting consent agreements prescribe maintenance and infrastructure solutions which the offenders agree to undertake and often include fines as incentives to comply.
The Clairton coke works has been the subject of eight consent agreements since 1990 that stemmed from complaints documenting thousands of air quality violations over that time.
Violations documented in the latest consent decree include emissions from doors and combustion stacks at each of the plant’s 10 coke oven batteries, and emissions that escape from charging ports and when coke is pushed from the ovens or transported as smoldering product. Corrections ordered in the decree include inspecting the walls of more than 120 ovens in three leaky coke oven batteries and fixing those in disrepair.
U.S. Steel was fined more than $3.9 million, but received nearly that amount in credit for fines previously paid for violating earlier consent agreements at Clairton. New fines levied total only $25,000.
“That’s not an incentive for compliance,” said George Jugovich, vice president of legal affairs for PennFuture. “It’s just pay to play for U.S. Steel because the fines aren’t set high enough. Otherwise, they’d be in compliance by now.
“These consent decrees are supposed to have a deadline and find mechanisms for you to comply. If you can’t comply, you need to go out of business. The public is not supposed to be carrying the burden of your noncompliance by suffering the health effects.”
The size of the fines imposed on polluters was criticized as “not large enough to serve as an effective deterrent” by the county Office of the Controller in an audit of the health department Air Quality Program last year. The findings are based on an analysis of violations and fines against the Clairton plant and the now-closed Shenango, Inc. coke works.
Such criticism doesn’t account for the investments in infrastructure and repairs companies make to correct the problems they are ordered to solve in consent agreements, including the most recent one, said Allegheny County Air Quality Program Chief Jayme Graham. “For this consent order, every wall they build will probably cost close to $1 million. The work that is required is what’s important about these consent orders. What we want are the controls.”
Company investment, technological advances, oversight, tighter regulations, enforcement actions and persistent environmental advocacy all have contributed to improving regional air quality over the past 20 years, including in the Mon Valley. At the Liberty Borough air monitor—the best indicator of PM2.5 coming from the Clairton plant—annual levels stand at 12.9 micrograms per cubic centimeter, slightly above the current federal standard. In 2002 the PM2.5 annual average at the same monitor was 21 micrograms per cubic centimeter.
PM2.5 levels fell significantly after the modern C-Battery went online in 2012 replacing three 1950s-era batteries. U.S. Steel had also agreed to build D-Battery, a second environmentally advanced network of coke ovens with the potential to lower particulate pollution even more.
But the company later told the county it couldn’t afford to build another modern coke battery and agreed, instead, to install two less-expensive low-emission quench towers as a trade-off. The cancelled D-Battery was to replace Batteries 1, 2 and 3—batteries built in the mid-1950s that emissions data show to be among the dirtiest at the plant.
“We agree that our shared environment is a resource that must be protected and preserved,” U.S. Steel spokeswoman Erin DiPietro said. “However, it is critical to maintain the balance between environmental responsibility and economic opportunity for our region.”
The Clairton plant hasn’t been as protective of the environment as local and federal regulations require. The challenges of doing so are daunting. Its track record is one of improving, but falling short. The question is whether North America’s largest coke works, and the last one operating in the region, can ever fully abide by the letter of the law. “Looking at recent compliance records, I can affirm it is possible, and likely, the company can operate without violations, even though there are so many emission points and regulations,” said Allegheny County’s Graham. “But it takes effort and intention on the part of all the operations and management staff to maintain compliance.”