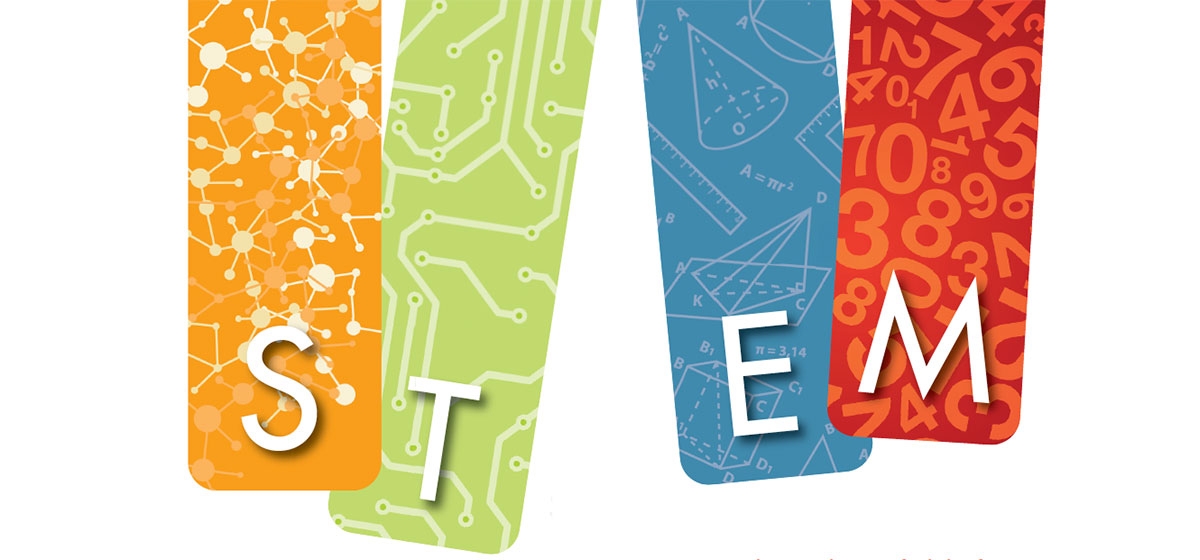
In the decade ending in 2020, United States employers will create about 2.1 million jobs in science, technology, engineering and math (STEM) as well as the professional sector, according to the federal Bureau of Labor Statistics. As America moves to assert or retain leadership in such fields as robotics, unconventional energy plays and next-generation computers and telephony, that’s great news.
Or is it? What happens if the nation’s educational system can’t produce enough STEM-trained people to fill those jobs? Will the U.S. fall back in all those technology-based fields and see erosion of its competitive standing in international commerce? Will those jobs, and the businesses that produce them, migrate offshore?
Welcome to the STEM Gap—the STEM Crisis, some style it—which has America’s business and education sectors scrambling to find ways to make technical careers more palatable to students and young job seekers. The phenomenon has ramifications for Pittsburgh-area employers, many of whom embraced and implemented new technologies to remain globally competitive and now must find the talent to operate and improve those tools.
With this article, we kick off a three-part series on the STEM Gap and its impact, now and long term, on the region. Below: what local companies are doing to stem the tide.
It wasn’t too many years ago that, when Bayer Corporation advertised openings at its Houston-area plant in Baytown, Texas, it was inundated with thousands of resumes. Today, those same postings will attract as few as 200 responses.
“We often can’t find people with technical training,” says Rebecca L. Lucore, chief-of-staff for Bayer MaterialScience LLC (NAFTA region). “Houston is the hub of the energy sector, and we’re having to compete for people like you can’t believe.”
That’s a concrete manifestation of the STEM Gap that American employers face as they strive to remain competitive in an increasingly global economy. Some organizations that have studied the situation paint the shortage of young talent with STEM training in draconian terms: our fiercest international rivals will eat our lunch, then make us wash the dishes.
Consider just some of the gloomy statistics. The National Math + Science Initiative indicates that only 45 percent of 2011 U.S. high school graduates were ready for college-level math; in that same cohort, only 30 percent were prepared for college-level science. The U.S. Navy’s STEM2Stern project reports that only 4.4 percent of undergraduate degrees in the U.S. are awarded in engineering; the global average is 13 percent.
Even when high school graduates begin STEM studies in college, they abandon them at alarming rates. Undergraduate programs in science and engineering experience the lowest retention rates among all academic disciplines, according to the National Center for Education Statistics and the National Science Board, with fewer than half of undergraduates who declare an intent to major in a STEM field completing a degree in one of those subjects.
That’s not the case in China where, says the National Math + Science Initiative, 31 percent of all bachelor’s degrees in 2008 were awarded in engineering. In the U.S., that figure was 4 percent. In western Pennsylvania, the STEM Gap is the joker in prosperity’s deck. Last year, the Allegheny Conference on Community Development released the results of a survey of 37 companies in the region’s burgeoning energy sector and identified 14 target jobs—ranging from petroleum engineers to machinists to welders and solderers—that would be both critical and difficult to fill. Respondents indicated they are highly confident in their ability to fill only one of every five openings in the key categories.
“The most common reason for their lack of confidence was the deficiency in technical and/or professional skills required to perform those jobs,” the report says.
Laura S. Fisher, senior vice president for the Conference, notes that the STEM Gap here may have its roots in the decline of the heavy metals industry a generation ago.
“At the regional level, 30 years ago, we hit rock bottom,” Fisher says. “We had an 18 percent unemployment rate, and we hemorrhaged people for a decade or two. We weren’t hiring, and demand for STEM-related degrees evaporated. So we saw huge shortages in fields like engineering. There weren’t a lot of jobs in the pipeline, so people didn’t choose to become engineers.”
Now that there are jobs in the pipeline, there may not be enough qualified people to fill them. Says Ann Dugan, executive director of the Institute for Entrepreneurial Excellence at the University of Pittsburgh: “You talk to any employer—they have jobs, they just can’t fill them. There’s a disconnect between students getting out of college or high school and the skills they need to get work.”
Managing the gap
So how are local employers managing the STEM Gap? Passably, although many have adopted new approaches to nurture and recruit young STEM talent.
“We’re not seeing too much of an issue getting STEM-trained folks into the organization,” says Jill DePompei-Morales, human resources manager for Chevron Appalachia. “The only time we’ve seen a little bit of a drag is when we have multiple openings on the petroleum engineering side.”
Westinghouse Electric Co. has been on a hiring binge over the past five years—more than 6,000 new employees—and has been able to fill the positions with recent grads and mid-career workers with some experience in nuclear energy or related industries. Yet Leigh A. Pogue, vice president of human resources business partners for Westinghouse, knows there are treacherous waters ahead, particularly as the company’s workforce ages.
“With Marcellus Shale, we’ve experienced some competition for the same talent,” Pogue notes. “It’s important that there’s a sufficient supply to feed our company, our customers and other parts of the energy sector looking for the same people. So we see talent demand as a very important issue.
“Somewhere between 10 percent and 20 percent of our workforce, depending on what region of the world you’re in, can retire today. Our projection is we’ll have another couple thousand people who can retire within the next 10 years. The good or bad news is that the economy has helped us in that a lot of people who could have retired have chosen not to.”
Among large local employers, NOVA Chemicals has an unusual perspective on STEM. While it maintains its U.S. commercial center in Moon Township and a manufacturing complex in Monaca, the bulk of its production capacity is in Canada. Kevin Watson, NOVA’s vice president, human resources, indicates that, whether it’s for the 5 percent to 6 percent annual attrition in Canada or the 2 percent to 3 percent yearly turnover here, Nova is feeling the STEM heat.
“We’re concerned,” Watson says, “concerned enough that we’re trying to take actions that won’t solve things overnight but will make us ready for the future.”
To meet the immediate need, however, NOVA has been hiring foreign nationals for positions—including some in treasury and information technology at Moon—that it can’t fill locally.
“Some unique candidates with the best skills are coming from offshore,” Watson says. “Unless you’re very specialized or very senior, those visas will run out. I totally understand the need to hire people in the U.S., but that does make it difficult. With a visa, you have a three-to-five-year window, and then they have to go. That’s clearly not optimal for us. Whenever someone in the organization wants to hire a person with a visa, I need to know about it because I know it’s generally only temporary.”
Not only are visas a stopgap solution, but they also can trap companies in a political thicket, as the number and types of visas the U.S. will grant always are the subject of heated debate on Capitol Hill.
“Before 9/11, it was hard to rely on visas,” Bayer’s Lucore observes. “It’s not even doable anymore. People aren’t able to get visas for extended amounts of time.”
PPG Industries has imported some talent, with mixed results.
“We’ve been able to keep some,” says Truman Wilt, PPG’s director of science and technology for optical and chemical products. “But developing countries are having an economic boom, so some qualified individuals are looking to return home.”
Partnerships aplenty
With visas iffy at best, many local businesses have found a better mousetrap—partnerships with educational institutions to make STEM careers more appealing to students while developing curricula more likely to produce grads with in-demand skills. In one of the most successful examples, the University of Akron introduced a degree program in corrosion engineering—billed as the first of its kind in the nation—to help meet the talent needs of its partner, PPG. The parties were brought together by the U.S. Department of Defense, which, Wilt says, “connected the dots.”
“A lot of things we work on in the private sector also are big issues for the government,” he added.
In Houston, Bayer offers internships to community college students, while in Berkeley, Calif., home of Bayer’s U.S. biotechnology center, the company has launched Biotech Partners to introduce students to the discipline.
“We target students who have shown potential,” Lucore reports. “We provide a mentor, extra science courses and internships. The program has a 98 percent graduation rate. They come out ready to work in our labs.”
Locally, the company and Duquesne University collaborate on the Bayer Scholars Program, which provides financial support and internships for women and other minorities chronically under-represented in STEM careers. In 2012, Bayer brought on three program alumnae as full-time employees.
In addition to its partnerships with colleges and technical schools, Westinghouse sponsors the Westinghouse Science Honors Institute, a Saturday program that brings kids to the company’s facilities, and the N-Vision Program, through which Westinghouse employees offer instruction and teacher workshops at local schools.
“It allows us to teach children in their formative years that nuclear energy is not something to fear but something to embrace,” Pogue says.
Beyond its participation in Reading Is FUNdamental Pittsburgh and the Carnegie Science Center’s Chevron STEM Center, NOVA has taken a different tack focused on employee retention. A new job classification called “senior technical positions” allows staff more room for professional growth—and a compensation bump. If those positions induce technical employees to stay on, NOVA will need fewer new hires.
“It used to be the only way to upgrade your pay was in senior leadership,” Watson says. “With senior technical positions, we’re creating avenues where good scientists can do what they love and still advance.”
Chevron Appalachia has a similar approach, offering its employees technical training at several points in their career development. “We’re getting our early-career folks up to speed technically as fast as we can,” DePompei-Morales says.
Still other companies, frustrated by the shortage of STEM talent, are hiring recent grads without STEM training and immersing them in crash courses.
“We’ve seen programs that are six months long and others that last only two weeks,” Pitt’s Dugan says. “Some of them target recent high school graduates while others recruit students during or right after college.”
In PPG’s version of this thrust, new hires are assigned mentors to help them develop appropriate STEM skills.
“For some skill sets we have not been able to find, we’ve opted to bring in people who may not totally have the qualifications we’re looking for and develop those people through in-house training,” Wilt says. “Some of them have met the expectations and reached our hopes. With others, we didn’t get there. It’s like an experiment. Each one is different, but you have to run it and see where it gets you.”
Thus, through a combination of outreach, innovation and hustle, local employers are bridging the STEM gap—for now. But what happens in the future?
“If we can’t find an influx of new people,” Pogue predicts, “we won’t be able to meet the need.”