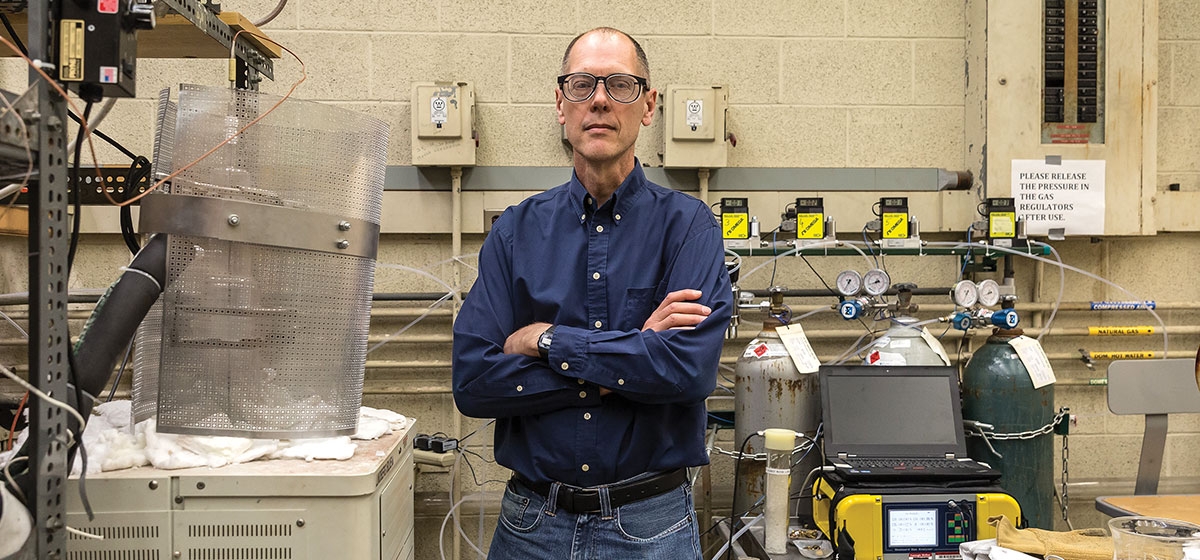
Power companies aren’t alone in their shift away from coal. Steelmakers, industry groups and the federal government are spending millions looking for a way to make steel without coke, the carbon-rich form of coal used to fuel blast furnaces. Like coal-fired power generation, coke production is a major source of air pollution, and its processing costs often make it the most expensive raw material fed into the furnace.
“Ever since coke was first used in a blast furnace, which I think was 1753, there have been attempts to try and run it without coke,” said Chris Pistorius, co-director of the Center for Iron and Steelmaking Research at Carnegie Mellon University. “To make iron in a blast furnace, you definitely need coke. How much coke you need, that’s an interesting question.”
As far back as 2009, U.S. Steel highlighted to its investors its use of natural gas to reduce the need for coke in its blast furnaces. The company’s coke production fell from 8 million tons in 2013 to 5.6 million in 2015 as it shuttered coke-making operations across the country, according to annual reports it filed with the U.S. Energy Information Administration.
U.S. Steel’s Clairton Works produces 4.3 million tons a year, which is almost one-third of all the coke produced in the U.S. in 2015, according to the U.S. EIA. It’s also perennially in violation of air quality standards and has been fined millions of dollars despite the company spending $600 million in upgrades meant to make it run cleaner.
“Over time, steel producers have discovered that alternative fuels, including natural gas, self-generated coke oven gas, and pulverized coal can be injected into the furnace to replace some of the coke,” said Meghan Cox, spokeswoman for U.S. Steel. “These options allow steelmakers to be flexible and improve their cost competitiveness based on raw materials costs, while reducing dependence on coal and coke.”
Coking plants consumed 4.6 million fewer tons of coal in 2016 than they did in 2010, a 21 percent drop, according to the U.S. Energy Information Administration.
Every kilogram of natural gas can replace a kilogram of coke, roughly speaking, Pistorius said. But that only works up to a point. Blast furnaces still need coke because it behaves in ways other materials don’t. When heated, it turns molten and flows; as some of the volatile compounds are cooked out of it, it becomes hard; and in between, it allows gas to flow through the blast furnace, he said.
“That’s quite unique,” Pistorius said. “Only coke can do that job, and there isn’t really an alternative.”
So, rather than a replacement fuel for the blast furnace, the industry is looking for a replacement for the blast furnace itself.
“We’re looking at technologies that will make major changes in steelmaking,” said Lawrence Kavanagh, president of the Steel Market Development Institute, a division of the American Iron and Steel Institute. The Institute is the main industry group for steelmakers in North America, with a membership that includes 19 steel producers including U.S. Steel, as well as 95 associate members.
“We’re looking at significant changes in production processes, cost of operations and environmental impact. The best [research] projects have all three,” said Kavanagh.
The institute and U.S. Department of Energy are spending $11 million on a multi-year research project at the University of Utah that creates hot metal from iron ore powder in a natural gasfired reactor. Using gas rather than coke could cut carbon emissions by 39 percent, according to the Energy Department.
“That’s at the very large laboratory scale,” Kavanagh said. “Testing of that technology is ongoing.”
Kavanagh declined to say what the institute spends on research overall, but its funding helped kick off another research project that, according to its lead scientist, produces no carbon emissions at all.
Called electrolytic steelmaking, the process requires no coal, emits no toxins, and produces oxygen as a byproduct, said Donald Sadoway, the John F. Elliott professor of materials chemistry at the Massachusetts Institute of Technology.
Sadoway’s process uses iron ore dissolved in an electrolytic—or electricity- conducting—solution. A pair of electrodes developed by his research team fire electricity through the solution, raising the temperature to 1,600 centigrade, or about 3,000 degrees Fahrenheit.
As in a blast furnace, the iron ore melts and hot metal makes its way to the bottom of the chamber. Unlike a blast furnace, the process uses no carbon for fuel and so produces no carbon dioxide, he said. “No only do you not generate carbon dioxide and all the other side emissions; for every ton of liquid iron you produce, you get two-thirds of a ton of industrial oxygen.”
To keep the process carbon-free, a steel plant using Sadoway’s technology would have to get its electricity from renewable power. “Obviously, you don’t want to take a wrecking ball to a blast furnace and then use coal to generate the electricity,” Sadoway said. But the technology raises the possibility of a solar-powered steel mill. “When the sun shines, you make metal. When the sun doesn’t, you tell people to go home and spend time with their families.”
Sadoway’s company, Boston Electrometallurgical Corp., built a “pilot-scale reactor” in a Boston suburb that has produced “tons” of steel, he said. “This is not a science experiment.”
The American Iron and Steel Institute stopped funding the project several years ago because of doubts about whether it would be cheaper to produce steel in that manner, but they continue to monitor Sadoway’s progress, Kavanagh said.
The scale and economics of steelmaking mean new methods of steelmaking have a high bar to clear before they’re adopted, Sadoway said. Steelmakers have spent billions of dollars on equipment for a manufacturing process with coke at its core.
Sadoway believes that inertia is likely to be a major obstacle to the industry adopting his method. “The process is so different. They look at all that capital investment and say, ‘You mean we don’t use all of this anymore?’”
New methods of steelmaking also have to compete with blast furnaces that are the products of more than 300 years of refinements. “Because the blast furnace has been around for so long, it’s been optimized,” Pistorius said. “It is very energy efficient. That makes it hard to improve upon.”