A Model of Respect
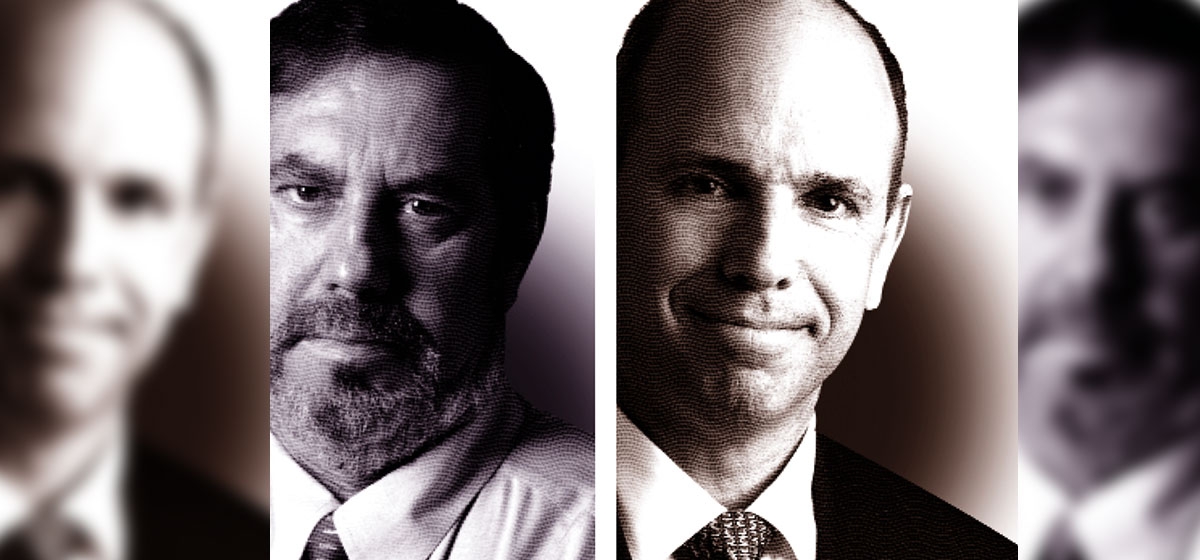
At a time when organized labor is under attack and manufacturing is crawling to its feet after a dramatic recession, two major players, John Surma, CEO of U.S. Steel, and Leo W. Gerard, international president of United Steelworkers, met on the North Side campus of Community College of Allegheny County to discuss the future.
It was the first of a series of lectures, called “Pittsburgh Labor and Management Past and Present.”
The two share common backgrounds and respect for each other. Surma was born in McKees Rocks, in the working-class area called The Bottoms, and Gerard hails from Sudbury, Canada, the son of a union miner. As Surma said, “We have often commented that, if one of us had taken a different turn and I ended up in his position and he in mine, things would probably be about as they are now.”
U.S. Steel and the USW grew from the fiery furnaces and confrontations of the 19th century, and the relationship is a mature labor-management culture, says Charlie McCollester, retired Indiana University of Pennsylvania labor history professor. “After all, we’ve been at this 150 years; it’s like a long-term marriage. You learn to negotiate.” As Gerard put it, “Our union was formed in 1932, and the first agreement signed was with U.S. Steel, upheld with the good word of the two leaders. Through all the years, we have had two labor disputes, one in 1959, and one in 1986—a positive track record for collective bargaining. We use our model with U.S. Steel to work with other industries.”
Below are highlights of the discussion.
labor-management relations:
gerard: “John is the only person in a major steel company who sat through a complete round of bargaining with our union. In 2003, we had just worked with U. S. Steel on the acquisition of the bankrupt National Steel. At the time John was chief financial officer of U. S. Steel. We were going through a period of tremendous anxiety, and weren’t sure where the industry was going to land.”
surma: “I decided at that time that the union–management relationship of our company was so embedded in our DNA that I would never understand the soul of our company if I didn’t understand that relationship. The best way I could do it was to be at that table, and it was one of the most exhilarating experiences of my career. We got a contract that allowed us to unleash the productivity of our workers. Leo’s leadership at that time was visionary and courageous.”
gerard: “In that bargaining, we negotiated a public policy agreement that we would work together to promote manufacturing in America. We formed the Alliance for American Manufacturing to defend industry, to educate officials at every level on the importance of manufacturing.”
fair trade:
surma: “We like trade, when it is fair. But the playing field was tilted against us. [In 2008] we were overwhelmed by imports from China, and when our rights are interfered with, we take action. Leo and I were the star witnesses before the International Trade Commission—you can imagine what that was like—and we won. They really know we’re tough, when we go together. Because of that case, we got 1,000 people back to work.”
surviving crises:
gerard: “In 2002, the U.S. steel industry was under attack by unfairly traded steel, and the industry went through 50 bankruptcies. Had it not been for the alliance we formed, I’m not sure the industry would have survived. At a time when manufacturing was at its strongest, 25 percent of GDP, people were trying to tell us that we could have a robust economy selling services to one another. We graduated more financial engineers than mechanical engineers. I can remember having discussions with John about wanting to invest in the steel industry, and Wall Street wanted a premium on the money that they would lend. Yet at the same time, if you had some idea about a new technology or investing in the Asian Tigers, they would throw money at you. If you think your way through that, we can think of the period of long collapse, the collapse of the Asian Tiger [Hong Kong, Singapore, South Korea and Taiwan], the savings and loan collapse, the collapse of Russian and South American economies. All that time, those economies were dumping their steel in the U.S., driving us out of business.”
surma: “In 2008, when the financial crisis occurred, demand for our products fell by 50 percent. Half of our business dried up. We had 10,000 people on layoff, and I didn’t get a good night’s sleep for two years.”
gerard: “I remember, with some sense of pride, John telling me about the investments he wanted to make in Allegheny County. Within weeks of the groundbreaking for the improvements to the Clairton Coke Works came the economic collapse of 2008, and we were having a discussion with the company about whether the money would go into the pension plan or the coke plant. In the last quarter of 2008, our members made $12.86 per hour in profit sharing. In the first quarter of 2009, they made zero. Now that wasn’t the fault of the company or the workers; that was a bunch of skullduggery on Wall Street. It was because people had taken their eye off the prize. And the prize for America is a growing, vibrant, productive, secure, economy where people go to work in a safe place and put something away for their retirement.”
surma: “Since 1999, 40,000 manufacturing facilities have closed in this country. About 4 million manufacturing jobs were lost. Those facilities were our customers, and those jobs belonged to your neighbors and family members. At the end of World War II, manufacturing was 25 percent of our GDP; today it’s about 10 percent. There are 11 million jobs in manufacturing, and 22.5 million in government. Personally, I’d rather it be the other way around. Manufacturing is one of the ways to create wealth, not just redistribute it. Manufacturing provides jobs where you can have a vacation, a home, maybe a new car once in a while, put your kids through college and have a decent dignified retirement.”
pensions & healthcare:
surma: “Legacy costs are a complex issue. It has to be affordable to the provider and reasonable to the receiver. Since 1902, no one who ever worked for U.S. Steel—and that was 1 million people—left without honor and dignity. We have honored every pension and retirement agreement since 1902. Some companies have done otherwise. We’re not going to do that. This year we will spend $650 million on retiree pensions and health care. When I go the International Iron and Steel Institute meeting in a few weeks, people will be there from Japan, China, Korea and Brazil. I’m the only one who has to worry about those costs. There really has to be a change in the structure of healthcare. The system is not good for us.”
gerard: “We are both in some ways prisoners of the same system. We ought to have a healthcare system based on the basic principles of insurance, where the best way to distribute risk is to have the biggest pool possible, and that means everybody in.”